Gas-Tour
2. September 2015
Die nachhaltige Entwicklungsstrategie der Gazprom setzt die Erschließung neuer Märkte und eine Diversifizierung der Geschäftstätigkeit voraus. Daher gehört heute die Steigerung der Produktion von verflüssigtem Erdgas (LNG) und des Anteils auf dem LNG-Markt zu den Kernaufgaben des Konzerns.
Die günstige geographische Lage ermöglicht es Russland, Gas in alle Welt zu liefern. Der wachsende Markt der asiatisch-pazifischen Region wird in den nächsten Jahrzehnten zum größten Erdgasverbraucher. Zwei fernöstliche LNG-Projekte werden es der Gazprom ermöglichen, ihre Stellung in der asiatisch-pazifischen Region zu stärken: das bereits funktionierende Sachalin II und das im Bau befindliche Vladivostok LNG. Ein weiteres Projekt – Baltic LNG – zielt auf die Länder des Atlantik-Raums ab.
Wie Gas verflüssigt und als LNG transportiert wird, erfahren Sie aus unserer Bildreportage.
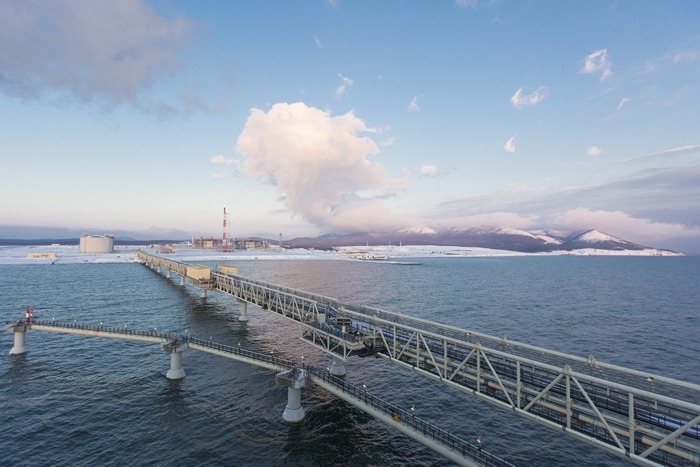
Das erste und bislang einzige LNG-Werk in Russland liegt in der Aniwa-Bucht im Süden des Verwaltungsgebiets Sachalin. Der Betrieb lieferte das erste LNG im Jahr 2009. Seitdem erfolgten bereits mehr als 900 LNG-Lieferungen nach Japan, Südkorea, China, Taiwan, Thailand, Indien und Kuwait (1 LNG-Standardlieferung = 65.000 Tonnen). Der Betrieb stellt jährlich mehr als 10 Millionen Tonnen Flüssiggas her und gewährleistet mehr als 4% LNG-Lieferungen weltweit. Dieser Anteil kann wachsen: Im Juni 2015 haben die Gazprom und Shell das Memorandum über den Bau einer dritten Produktionsstrecke des LNG-Werkes im Rahmen des Sachalin-II Projekts unterzeichnet.
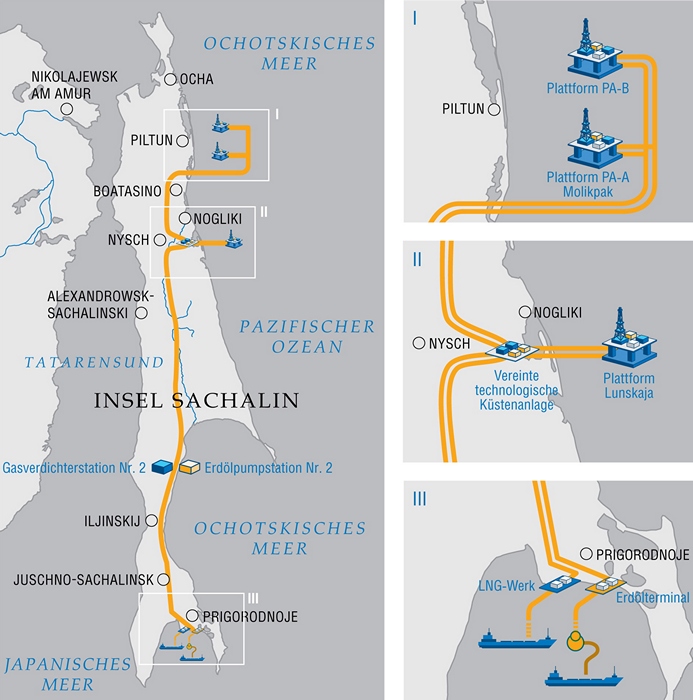
Betreiber des Sachalin-II Projekts ist das Unternehmen Sakhalin Energy, an dem Gazprom (50% plus 1 Aktie), Shell (27,5% minus 1 Aktie), Mitsui (12,5%) und Mitsubishi (10%) beteiligt sind. Die Sakhalin Energy erschließt die Erdgasfelder Piltun-Astochskoje und Lunskoje im Ochotskischen Meer. Die LNG-Fabrik bezieht das Gas vom Lunskoje Vorkommen.
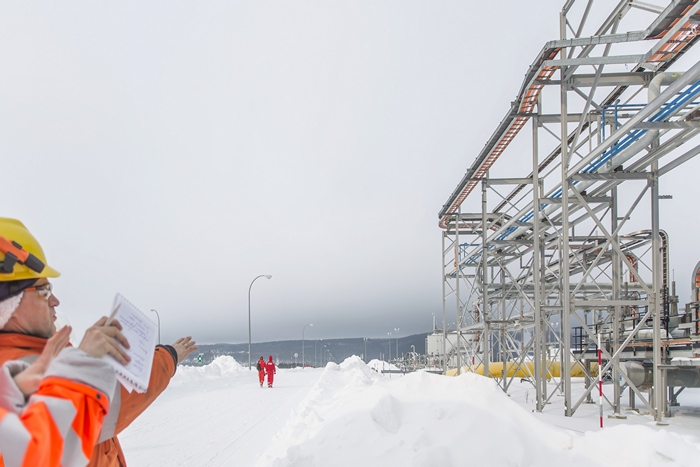
Das Erdgas legt eine Strecke von mehr als 800 Kilometern aus dem Norden in den Süden der Insel zurück und gelangt in den Betrieb durch das gelbe Rohr. Zunächst werden in der Gasmessstation Beschaffenheit und Volumen des angelieferten Erdgases geprüft, anschließend wird es zur Reinigung weitergeleitet. Der Rohstoff muss vor der Verflüssigung von Staub, Kohlendioxyd, Quecksilber, Schwefelwasserstoff und Wasser, das bei der Erdgasverflüssigung gefriert, gereinigt werden.
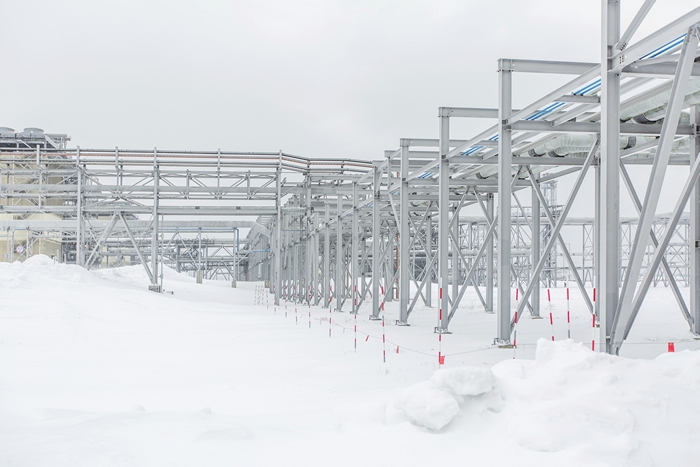
Hauptkomponente des LNG ist Methan, dessen Gehalt nicht unter 92% liegen darf. Das getrocknete und gereinigte Rohgas gerät anschließend auf die Produktionslinie, auf der seine Verflüssigung beginnt. Dieser Ablauf erfolgt in zwei Phasen: Das Gas wird anfangs bis auf minus 50 Grad und anschließend bis auf minus 160 Grad Celsius heruntergekühlt. Nach der ersten Kühlphase werden schwere Komponenten – Ethan und Propan – entfernt.
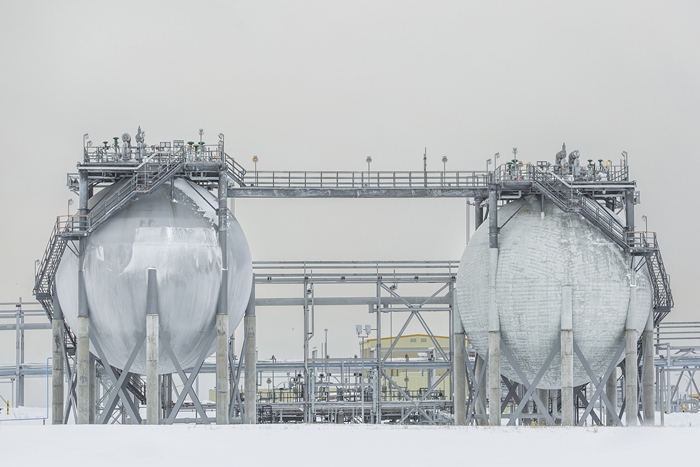
Ethan und Propan werden daraufhin in diesen beiden Tankbehältern eingelagert (Ethan und Propan werden in den weiteren Verflüssigungsphasen benötigt).
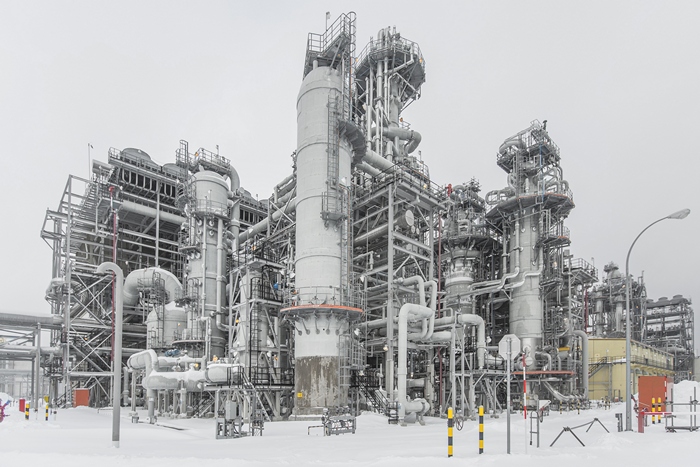
Diese Säulen sind die Hauptkühlanlage der Fabrik: Hier bildet sich das Flüssiggas bei einer Temperatur von minus 160 Grad. Das Gas wird nach einem Verfahren verflüssigt, das für diesen Betrieb exklusiv entwickelt worden ist. Es besteht im Wesentlichen darin, dass das Methan anhand eines Kühlmediums – Ethan und Propan – das aus dem Rohgas vorher abgesondert worden ist, gekühlt wird. Die Verflüssigung erfolgt bei normalem Luftdruck.
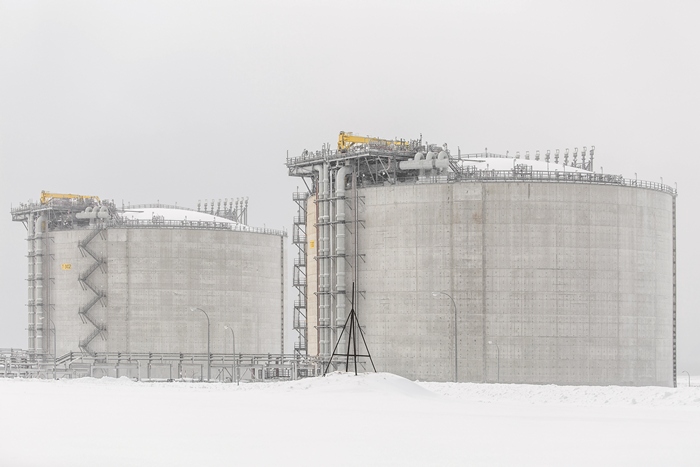
Das Flüssiggas wird in zwei weitere Tankbehälter gepumpt, in denen es wiederum unter Normaldruck bis zu seiner Verladung in einen Flüssiggastanker gelagert wird. Diese beiden Bauwerke sind 38 Meter hoch und haben einen Durchmesser von 67 Metern, der Umfang eines jeden Tankbehälters beträgt 100.000 Kubikmeter. Ihre Konstruktion weist Doppelwände auf. Das Innengehäuse ist aus einer kältebeständigen Nickel-Stahl-Legierung und das Außengehäuse aus vorgespanntem Eisenbeton gefertigt. Der anderthalb Meter breite Hohlraum zwischen den Gehäusen ist mit Perlit (vulkanisches Gestein) ausgefüllt, der die erforderliche Temperatur im Innengehäuse des Tankbehälters gewährleistet.
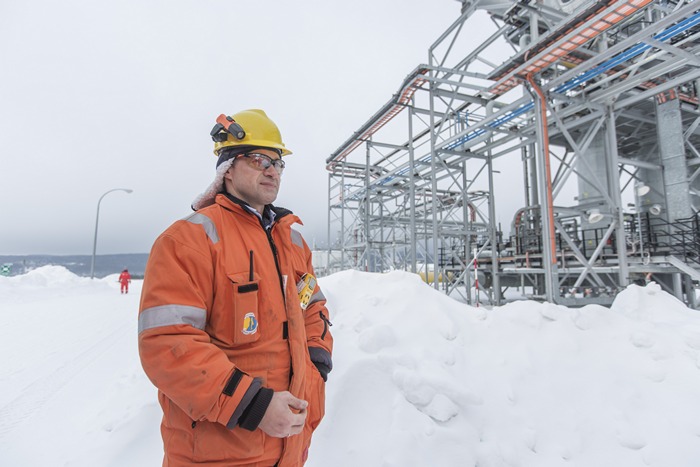
Die Führung durch die LNG-Fabrik machte für uns der leitende Ingenieur des Betriebes Mikhail Shilikovsky. Er stieg 2006 im Unternehmen ein und nahm an den abschließenden Bauarbeiten sowie an der Inbetriebnahme des Werks teil. Heute hat die Fabrik zwei Produktionslinien, auf denen jeweils bis zu 3.200 Kubikmetern LNG pro Stunde herstellt werden. Die Aufteilung der Produktion ermöglicht es, den Arbeitsablauf energiesparend zu gestalten. Aus demselben Grund wird das Gas schrittweise heruntergekühlt.
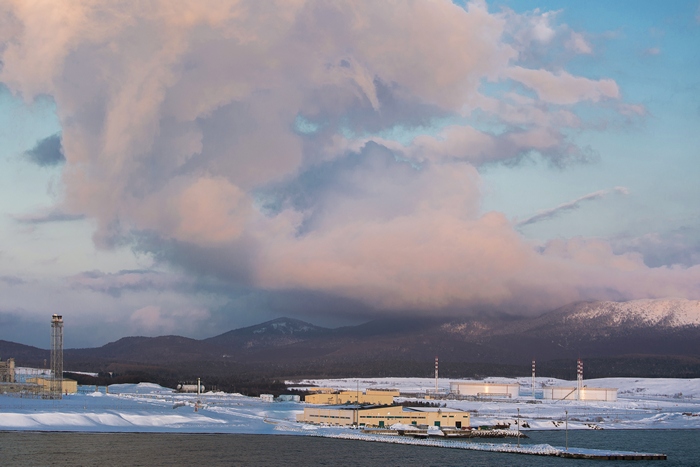
Fünfhundert Meter von der LNG-Fabrik entfernt liegt das Erdölterminal. Es ist wesentlich einfacher ausgestattet. Denn hier wird das Erdöl praktisch bis zum Versand an die einzelnen Käufer zwischengelagert. Das Erdöl gelangt in den Süden von Sachalin ebenfalls aus dem Norden der Insel. Es wird im Terminal mit Gaskondensat, das bei der Gasaufbereitung für die Verflüssigung abgesondert worden ist, vermischt.
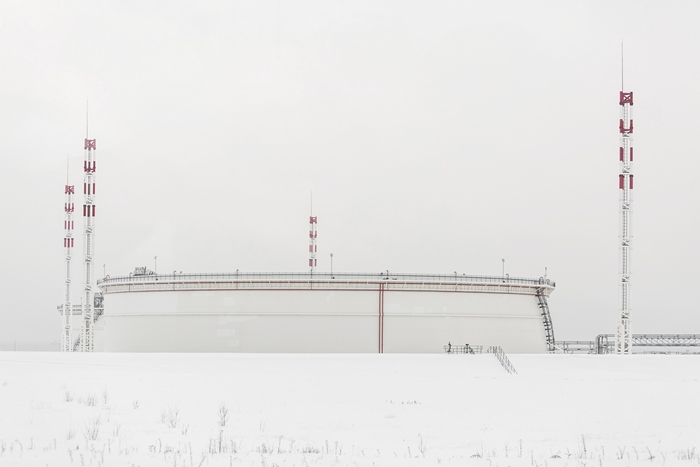
Das „schwarze Gold“ wird in zwei solchen Tankbehältern mit einem Umfang von je 95.400 Tonnen gelagert. Die Tankbehälter sind mit einem schwimmenden Dach ausgestattet: Wenn wir sie aus der Vogelperspektive betrachten würden, wäre der Erdölstand in jedem von ihnen zu sehen. Um die Tankbehälter vollständig mit Erdöl zu befüllen, benötigt man etwa 7 Tage. Deshalb erfolgt die Verladung von Erdöl einmal wöchentlich (LNG-Verladung – alle 2 bis 3 Tage).
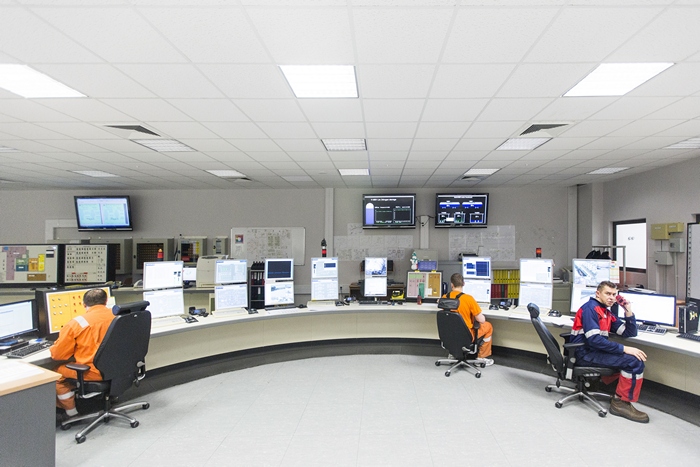
Sämtliche Arbeitsabläufe werden in der LNG-Fabrik und im Erdölterminal von dem Hauptbedienpult aufmerksam beobachtet. Alle Produktionsstätten sind mit Kameras und Sensoren ausgestattet. Das Hauptbedienpult ist in drei Teile gegliedert: Der erste ist für die Versorgungssysteme zuständig, der zweite überwacht die Sicherheitsanlagen und der dritte vollzieht die Arbeitsabläufe nach. Mit der Überwachung der Verflüssigung von Gas und dessen Verladung sind drei Personen betraut, von denen jede während ihrer Schicht (sie dauert 12 Stunden) bis zu 3 Kontrollschaltbilder je Minute prüft. Diese Arbeit erfordert ein gutes Reaktionsvermögen und Erfahrung.
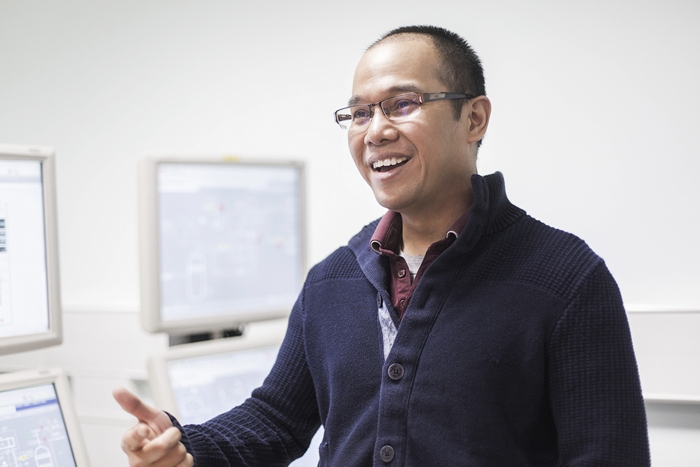
Zu den versiertesten Mitarbeitern gehört der Malaysier Viktor Botin (weshalb sein Vor- und Nachname so russisch klingen, weiß er selbst nicht so recht, sagt aber, dass ihn jeder, dem er begegnet, danach fragt). Viktor schult auf Sachalin bereits seit 4 Jahren junge Fachkräfte an Simuliergeräten des Hauptbedienpults, stellt ihnen jedoch reale Aufgaben. Die Schulung eines Neuanfängers dauert anderthalb Jahre, anschließend beobachtet der Ausbilder nochmal so lange dessen Arbeit „im Einsatz“.
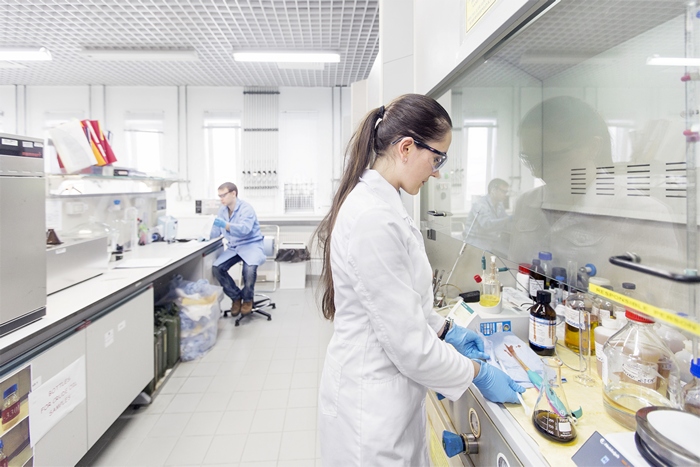
Mitarbeiter des Labors untersuchen indessen täglich nicht nur Proben des im Betrieb angelieferten Rohstoffs und die Zusammensetzung der für den Versand bestimmten LNG- und Erdöllieferungen, sondern auch die Qualität von Erdölprodukten und Schmierstoffen, die sowohl auf dem Fabrikgelände als auch extern verwendet werden. Auf diesem Foto sehen Sie, wie die Labortechnikerin Albina Garifulina die Beschaffenheit von Schmierstoffen prüft, die auf den Bohrplattformen im Ochotskischen Meer zum Einsatz kommen sollen.

Dies sind keine Untersuchungen mehr, sondern LNG-Tests. Auf den ersten Blick sieht Flüssiggas wie Wasser aus, es verdampft jedoch schnell bei Zimmertemperaturen und ist so kalt, dass man damit nicht ohne Schutzhandschuhe arbeiten kann. Der Test besteht darin, dass jedes Lebewesen bei der Berührung mit LNG erfriert. Auf der Chrysantheme im Glaskolben hat sich in nur 2 bis 3 Sekunden eine Eiskruste gebildet.
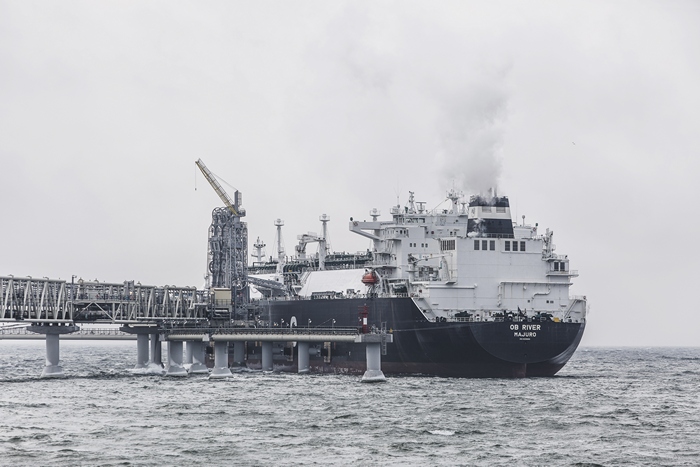
Inzwischen beginnt die LNG-Verladung. Der Hafen Prigorodnoje empfängt Flüssiggastanker mit unterschiedlichem Fassungsvermögen: von kleinen, die in einer Ladung 18.000 Kubikmeter LNG befördern können, bis hin zu so großen Tankern wie die Ob River, der auf dem Foto zu sehen ist und fast 150.000 Kubikmeter aufnehmen kann. Das Flüssiggas wird in die Tanks (so nennt man Behälter für die LNG-Beförderung auf diesen Schiffen) durch Rohre gepumpt, die unterhalb der 800 Meter langen Pier verlaufen.
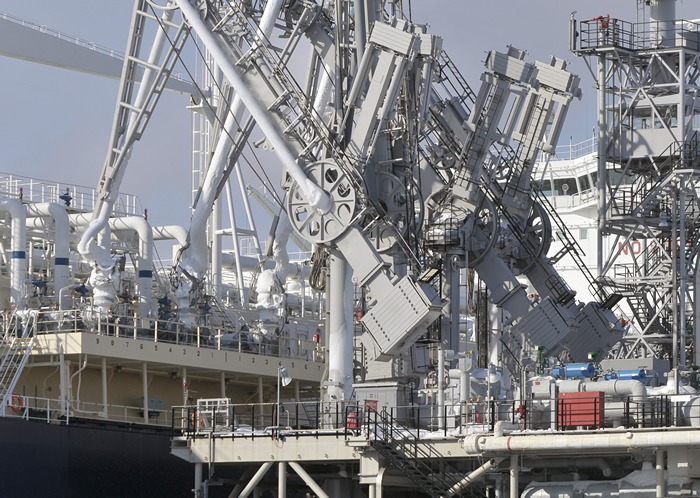
Die LNG-Verladung in so ein Tankerschiff dauert 16 bis 18 Stunden. Die Anlegestelle ist mit dem Schiff durch Tankschläuche verbunden. Das erkennt man sofort an der dicken Eiskruste auf dem Metall, die sich durch den Temperaturunterschied von LNG und Luft bildet. Zur warmen Jahreszeit bildet sich auf dem Metall eine noch größere Kruste. Archivbild.
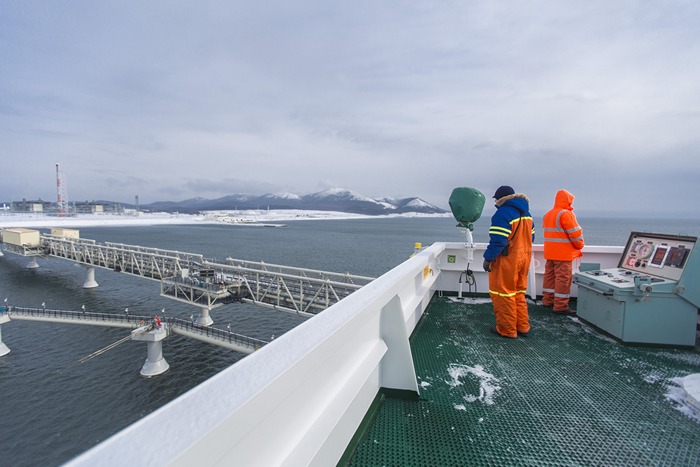
Das LNG ist verladen, das Eis geschmolzen, die Tankschläuche abgekoppelt, und nun kann die Reise beginnen. Unser Zielort ist der südkoreanische Hafen Gwangyang.
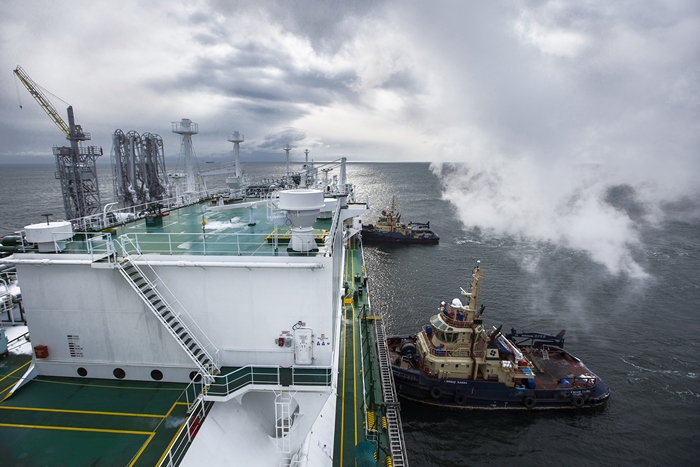
Da der Flüssiggastanker für die LNG-Verladung im Hafen Prigorodnoje mit dem Backbord anlegt, helfen ihm vier Schlepper, aus dem Hafen auszulaufen. Sie schleppen das Tankschiff buchstäblich hinter sich her, bis es wenden kann, um die Reise selbständig fortzusetzen. Im Winter müssen diese Schlepper auch die Einfahrt zu den Seebrücken vom Eis freihalten.
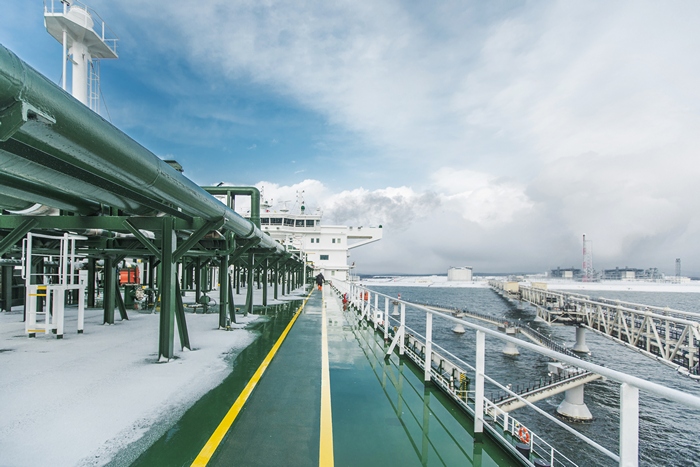
LNG-Tanker entwickeln höhere Geschwindigkeiten gegenüber anderen Frachtschiffen und umso mehr gegenüber Fahrgastschiffen. Die Höchstgeschwindigkeit des Flüssiggastankers Ob River beträgt mehr als 19 Knoten oder ca. 36 Kilometer pro Stunde (die Geschwindigkeit eines herkömmlichen Erdöltankers liegt bei 14 Knoten). Das Schiff kann die Strecke nach Südkorea in gut zwei Tagen zurücklegen. Da jedoch die dichte Zeitplanung der LNG-Terminals zum Ver- und Entladen zu berücksichtigen ist, werden die Geschwindigkeit und die Route des Tankschiffs korrigiert. Unsere Tour wird fast eine Woche dauern mit einer kleinen Rastpause vor der Küste von Sachalin.
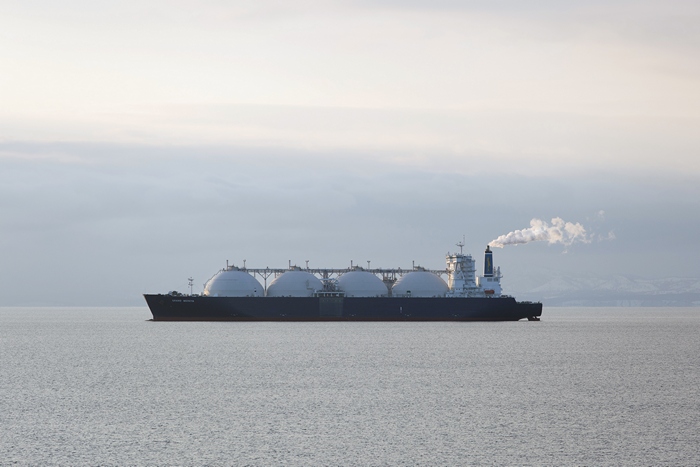
Durch diesen Zwischenhalt wird Brennstoff gespart und so ist er für alle Besetzungen der Flüssiggastanker zur Tradition geworden. Während wir vor Anker lagen und den geeigneten Zeitpunkt für die Weiterreise abpassten, wartete in unserer Nähe das Tankschiff Grand Merea darauf, dass es im Hafen von Sachalin anlegen durfte.
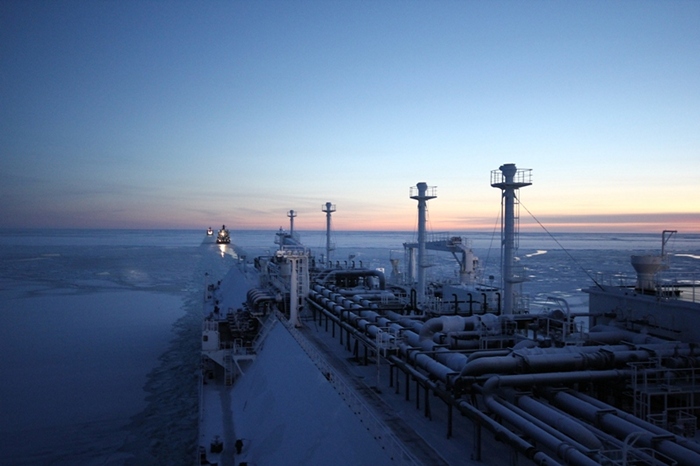
Nun wollen wir Ihnen aber ausführlicher über den Flüssiggastanker Ob River und seine Besatzung erzählen. Dieses Foto entstand im Herbst 2012, während der Beförderung der weltweit ersten LNG-Lieferung über die Nordostpassage.
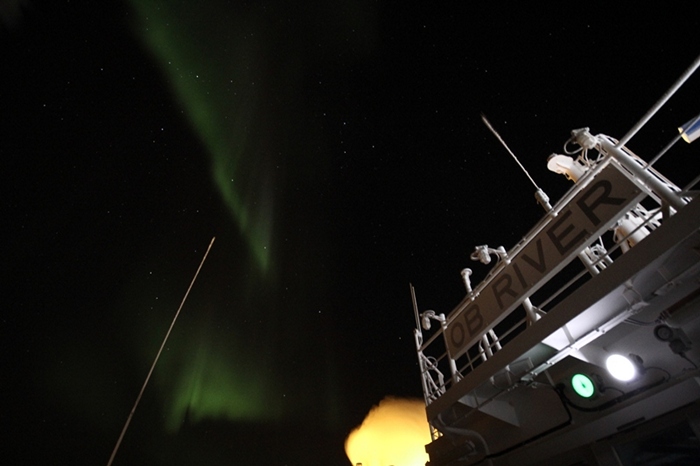
Die erste Reise unternahm nämlich der Tanker Ob River, der in Begleitung der Eisbrecher 50 Let Pobedy, Rossya und Vaygach sowie zweier Eislotsen eine LNG-Lieferung der Gazprom-Tochtergesellschaft Gazprom Marketing & Trading, abgekürzt GM&T, aus Norwegen nach Japan beförderte. Der Weg nahm fast einen Monat in Anspruch.
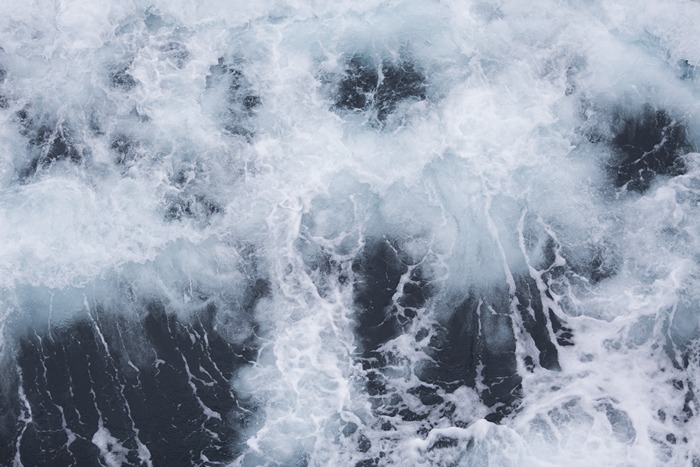
Der Medieninhalt kann nicht angezeigt werden, weil Sie der Cookie-Verwendung auf der Website gazprom.de nicht zugestimmt haben.
Akzeptieren Sie die Speicherung von Cookies gleich oder aktivieren Sie Cookies später mit entsprechenden Einstellungen.
Die Ob River ist von ihren Ausmaßen her mit einem schwimmenden Wohnviertel vergleichbar. Das Tankschiff ist 288 Meter lang, 44 Meter breit und hat einen Tiefgang von 11,2 Metern. Wenn man sich auf so einem riesengroßen Schiff befindet, erscheinen selbst zwei Meter hohe Wellen wie Spritzer, die an Bord platzen und phantasievolle Muster auf dem Wasser hinterlassen.
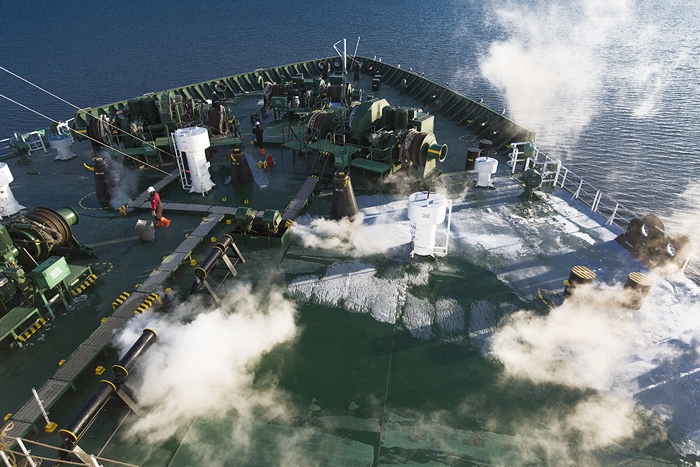
Der Flüssiggastanker Ob River erhielt seinen Namen im Sommer 2012, nachdem der Mietvertrag zwischen der Gazprom Marketing & Trading und der griechischen Reederei Dynagas abgeschlossen war. Zuvor führte dieses Schiff den Namen Clean Power und war bis April 2013 für die GM&T weltweit im Einsatz (unter anderem befuhr es zweimal die Nordostpassage). Anschließend wurde es von der Sakhalin Energy gechartert und wird nun bis 2018 im Fernen Osten eingesetzt.
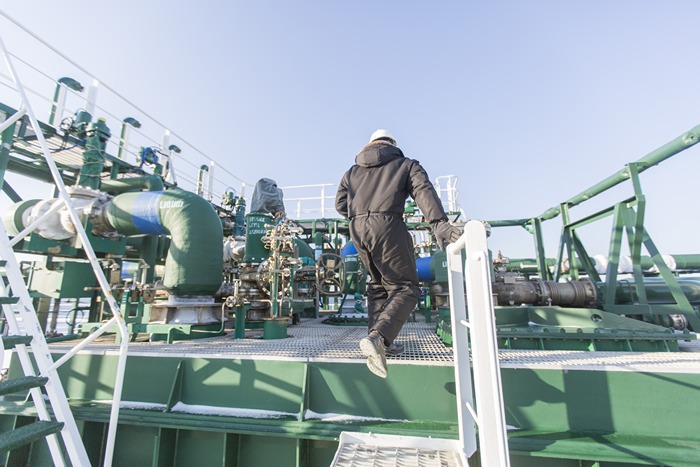
Die Membrantanks für das Flüssiggas befinden sich im Schiffsbug und liegen im Gegensatz zu den kugelförmigen Tanks (wie wir sie bei der Grand Merea gesehen haben) im Rumpf: Sie sind lediglich an den Rohren mit Ventilen zu erkennen, die über dem Deck aufragen. Die Ob River hat insgesamt vier Tanks mit einem Umfang von 25.000, 39.000 und je 43.000 Kubikmetern Gas. Jeder von ihnen wird höchstens zu 98,5% befüllt. Die LNG-Tanks haben ein mehrschichtiges Stahlgehäuse, die Hohlräume zwischen den Schichten sind mit Stickstoff befüllt. Dadurch kann die Temperatur des flüssigen Brennstoffs aufrechterhalten werden, und der Druck, der in den Membranen entsteht und höher ist, als im Tank selbst, schützt ihn gegen Schäden.

Auf dem Tankschiff ist auch eine LNG-Kühlanlage vorgesehen. Sobald das Frachtgut sich zu erwärmen beginnt, springt in den Tanks eine Pumpe an, die das kalte LNG vom Tankboden hochpumpt und es über die oberen Schichten des erwärmten Gases versprüht. So eine Selbstkühlung des LNG ermöglicht es, Verluste des „blauen Brennstoffs“ während des Transports zu minimieren. Diese Kühlanlage funktioniert jedoch nur während der Schifffahrt. Das erwärmte Gas, das sich nicht mehr abkühlen lässt, wird durch ein spezielles Rohr aus dem Tank in den Maschinenraum abgeleitet, wo es anstelle des Brennstoffs für das Schiff verbrannt wird.
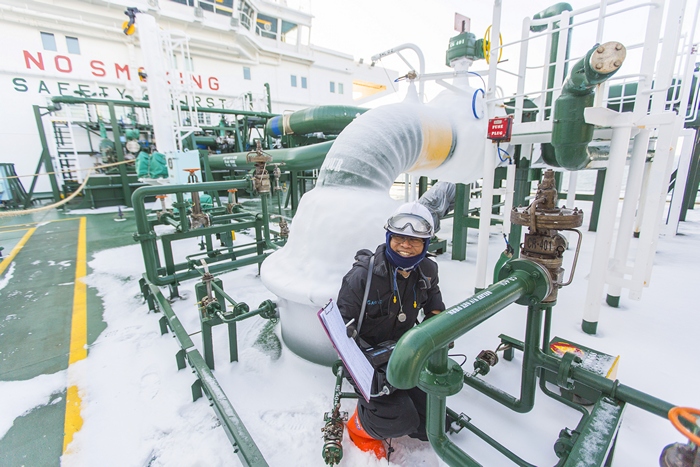
Gasingenieur Ronaldo Ramos beobachtet täglich die Temperatur und den LNG-Druck in den Tanks. Er prüft mehrmals am Tag die Anzeigen von Sensoren, die an Deck installiert sind.
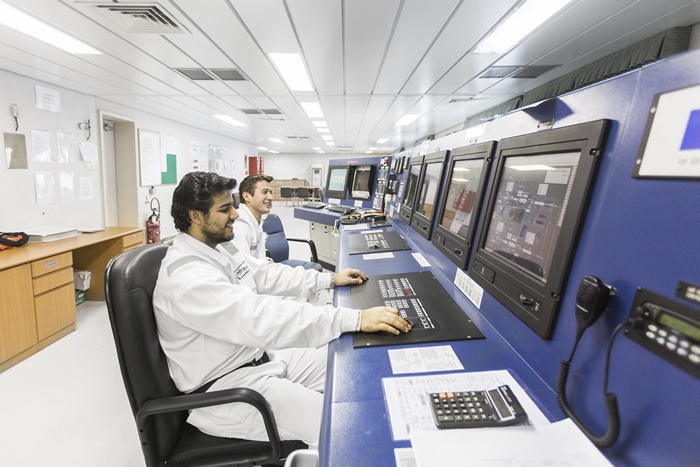
Eine gründlichere Analyse der Fracht nimmt der Computer vor. Am Bedienpult, an dem sämtliche erforderliche Informationen zum LNG vorliegen, haben der Erste nautische Offizier Pankaj Puneet und der Dritte nautische Offizier Nikolai Budzinsky Dienst.
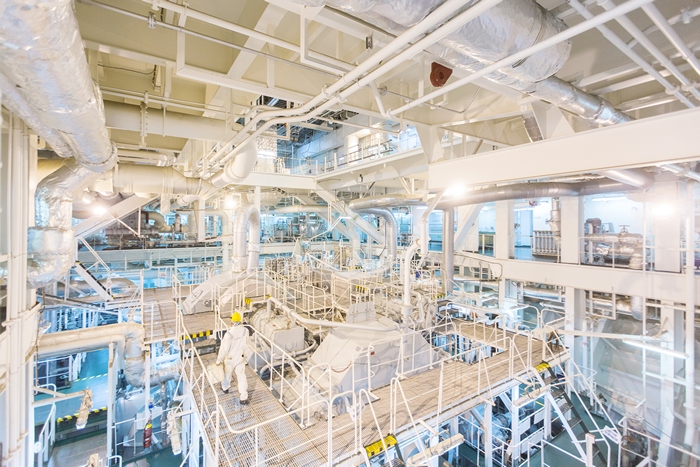
Dies ist der Maschinenraum, das Herz des Tankschiffs. An vier Decks (Geschossen) sind Motoren, Dieselgeneratoren, Pumpen, Kessel und Verdichter untergebracht, die nicht nur für die Fortbewegung des Schiffs, sondern für alle Versorgungsanlagen zuständig sind. Eine intakte Arbeit all dieser Vorrichtungen versorgt die Crew mit Wasser, Heizung, Strom und frischer Luft.
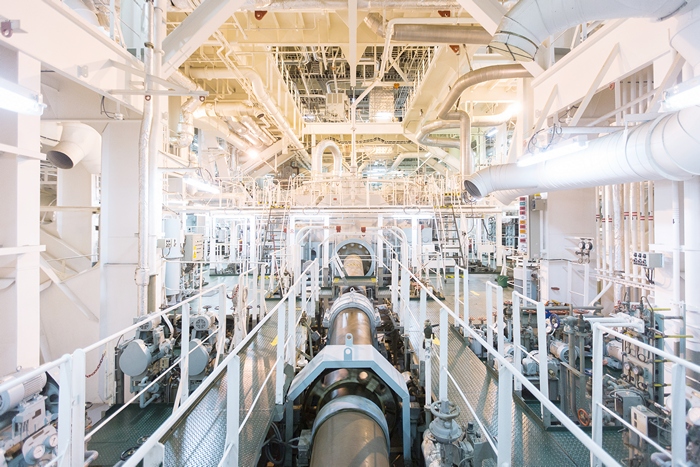
Der Medieninhalt kann nicht angezeigt werden, weil Sie der Cookie-Verwendung auf der Website gazprom.de nicht zugestimmt haben.
Akzeptieren Sie die Speicherung von Cookies gleich oder aktivieren Sie Cookies später mit entsprechenden Einstellungen.
Diese Foto- und Videoaufnahmen entstanden im tiefsten Innern des Tankerschiffs – fast 15 Meter unter dem Wasserspiegel. In der Mitte ist auf dem Bild die Turbine zu sehen. Sie wird durch den Dampf in Bewegung gesetzt und macht 4.000 bis 5.000 Drehungen pro Minute, wodurch sich die Schraube dreht und wiederum den Flüssiggastanker in Bewegung setzt.
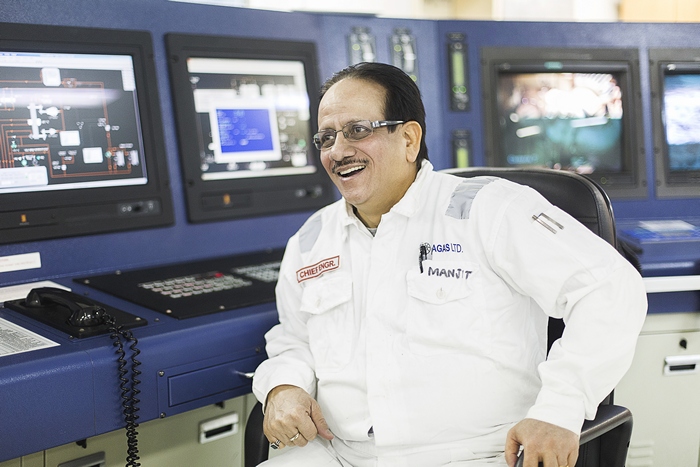
Darauf, dass auf dem Schiff alles pünktlich auf die Minute funktioniert, achten Mechaniker mit dem Chefmechaniker Manjit Singh…
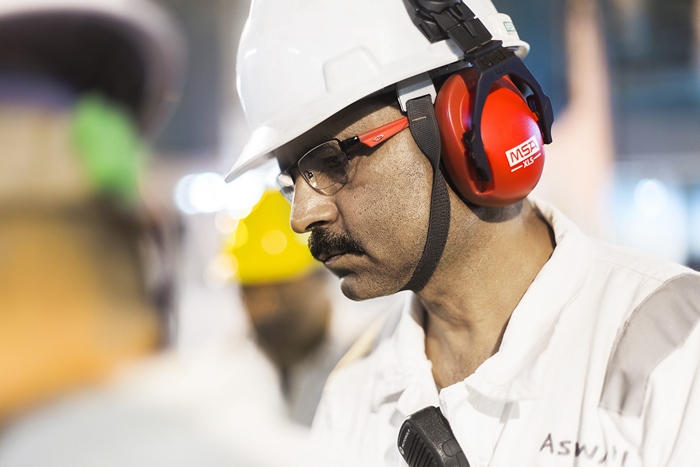
…und dem zweiten Mechaniker Ashwani Kumar an der Spitze. Sie stammen beide aus Indien, haben jedoch nach eigenen Schätzungen einen Großteil ihres Lebens auf hoher See verbracht.
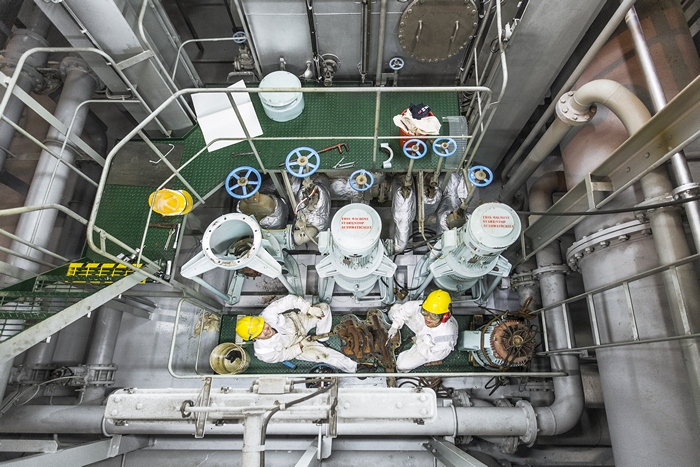
Die intakte Arbeit der Anlagen im Maschinenraum überwachen die ihnen unterstehenden Mechaniker. Sollte ein Gerät aussetzen, beginnen sie umgehend mit Reparaturen. Auch nehmen sie regelmäßige Wartungen einer jeden Maschine vor.
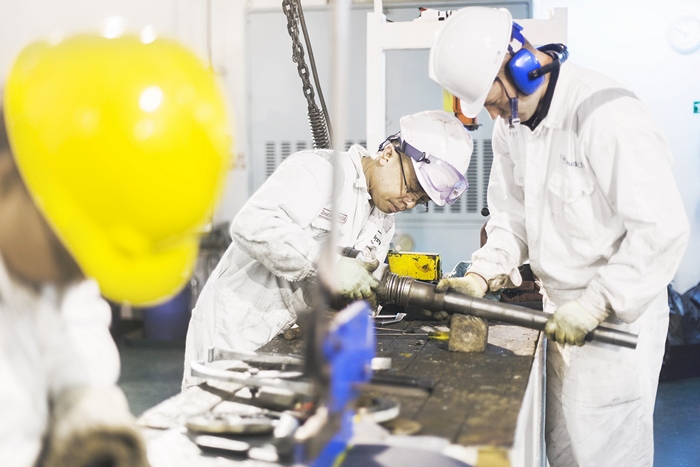
Was einer gründlicheren Arbeit bedarf, wird in die Reparaturwerkstatt gebracht. Die gibt es hier ebenfalls. Der dritte Mechaniker Arnulfo Ole (links) und der auszubildende Praktikant Ilya Kuznetsov (rechts) reparieren das Bauteil einer Pumpe.
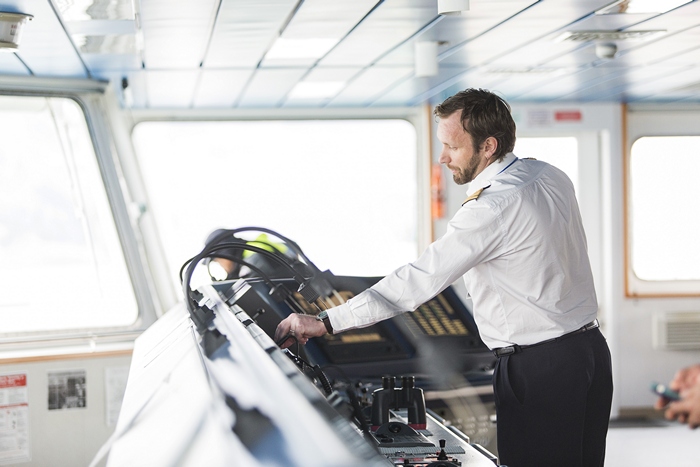
Das Gehirn des Schiffs ist die Kommandobrücke. Das Meer lockte Kapitän Velemir Vasilic bereits seit seiner frühen Kindheit: In jeder dritten Familie seiner Heimatstadt in Kroatien gibt es nämlich einen Seemann. Er stach bereits mit 18 Jahren in See. Seitdem sind 21 Jahre vergangen, er hat mehrere Dutzende Schiffe gewechselt und arbeitete sowohl auf Fracht- als auch auf Fahrgastschiffen.
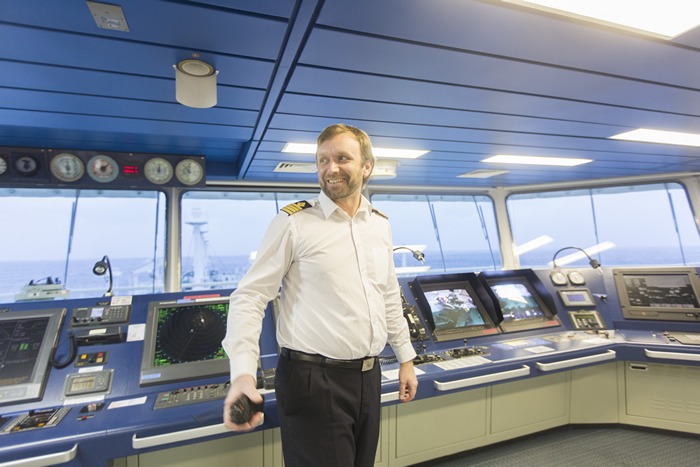
Aber selbst im Urlaub findet er immer wieder die Gelegenheit für eine Seefahrt, sei es auch nur mit einer kleinen Jacht. Er gesteht, dass er dort erst richtig die See genießen kann. Denn im Dienst hat ein Kapitän stets viel zu tun: Er ist nicht nur für das Tankschiff, sondern auch für jeden Mann in der Besatzung (sie zählt auf der Ob River 34 Personen) verantwortlich.
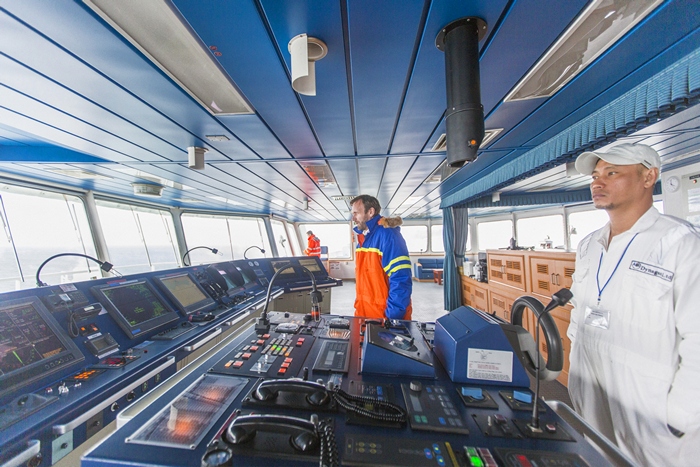
Die Kommandobrücke eines modernen Schiffs mit den vielen Anzeigetafeln, Geräten und verschiedenen Sensoren erinnert an das Cockpit eines Flugzeuges, selbst das Steuerrad ist ähnlich. Foto: Matrose Aldrin Galang wartet auf den Befehl des Kapitäns, bevor das Steuerrad übernimmt.
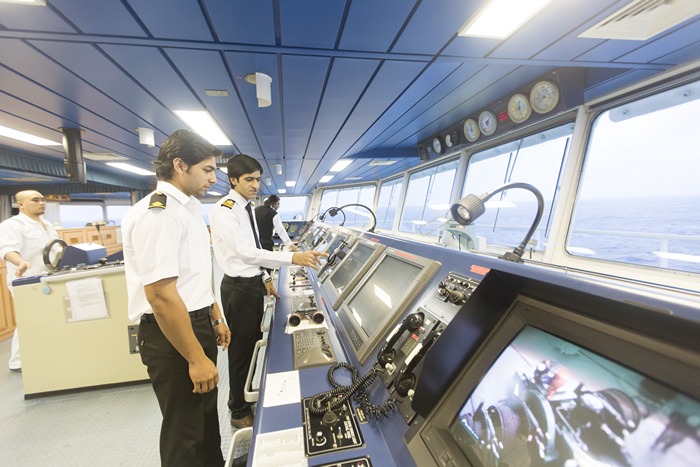
Der Flüssiggastanker ist mit Radaren, die den Typ eines Schiffes in seiner Nähe, dessen Namen und Besatzungszahl genau identifizieren, mit Navigationssystemen und GPS-Sensoren, welche die Lage der Ob River automatisch feststellen, mit elektronischen Seekarten, welche die zurückgelegte Strecke fixieren und die weitere Route abstecken, sowie mit elektronischen Kompassen ausgestattet. Allerdings halten erfahrene Seeleute die Jungen dazu an, sich nicht allein auf die Elektronik zu verlassen: Sie stellen ihnen hin und wieder die Aufgabe, die Schiffslage nach den Sternen oder der Sonne zu erkennen. Foto: Der Dritte nautische Offizier Roger Dias und der Zweite nautische Offizier Muhammad Imran Hanif.
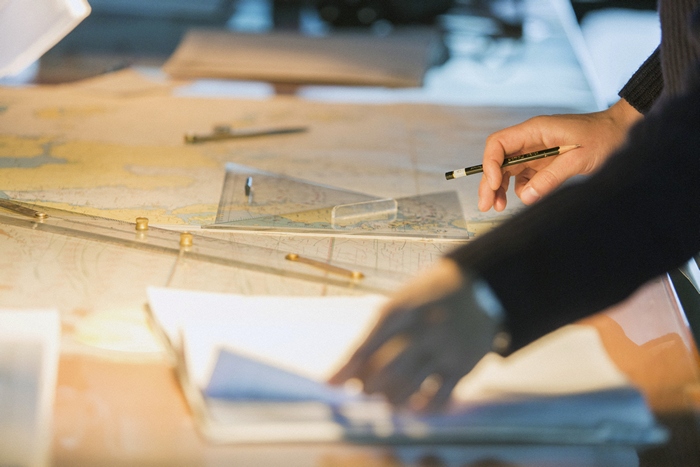
Dem technischen Fortschritt ist es bislang nicht gelungen, Seekarten auf Papierträger, auf denen die Lage des Tankschiffs alle Stunde mit Bleistift und Lineal vermerkt wird, und das Logbuch, das ebenfalls handschriftlich ausgefüllt wird, zu verdrängen.
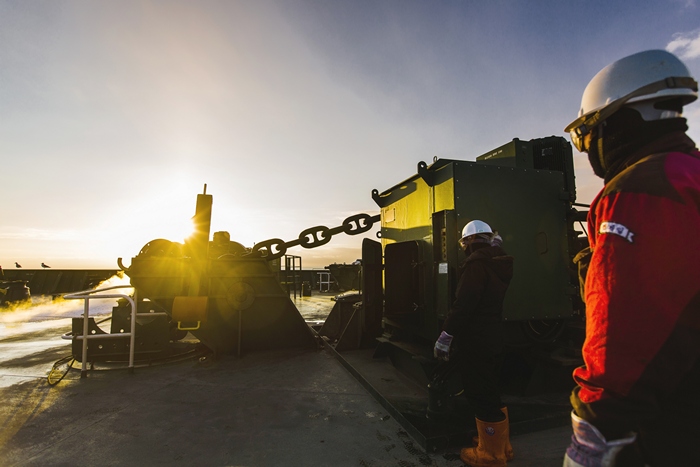
Der Medieninhalt kann nicht angezeigt werden, weil Sie der Cookie-Verwendung auf der Website gazprom.de nicht zugestimmt haben.
Akzeptieren Sie die Speicherung von Cookies gleich oder aktivieren Sie Cookies später mit entsprechenden Einstellungen.
Der Medieninhalt kann nicht angezeigt werden, weil Sie der Cookie-Verwendung auf der Website gazprom.de nicht zugestimmt haben.
Akzeptieren Sie die Speicherung von Cookies gleich oder aktivieren Sie Cookies später mit entsprechenden Einstellungen.
Nun ist es an der Zeit unsere Reise fortzusetzen. Der 14 Tonnen schwere Anker der Ob River wird gelichtet. Die fast 400 Meter lange Ankerkette wird von speziellen Maschinen hochgezogen. Dabei passen mehrere Besatzungsmitglieder auf.
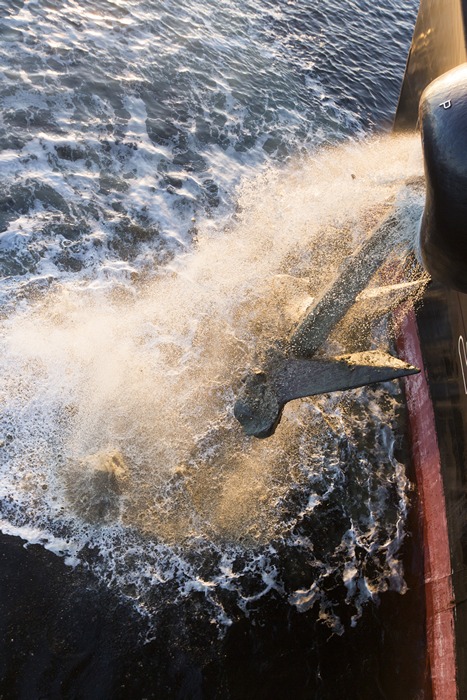
Für den gesamten Ablauf haben sie höchstens 15 Minuten. Die Crew will erst gar nicht darüber rätseln, wie lange der Vorgang in Anspruch nehmen würde, wenn der Anker manuell gelichtet werden müsste.
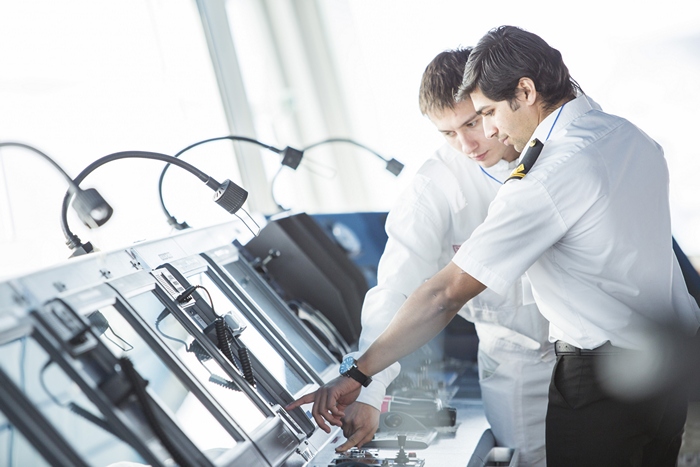
Erfahrene Seeleute sagen, dass das Leben auf dem Schiff sich heute von dem von vor 20 Jahren gravierend unterscheidet. Heute geht es vor allem um Disziplin und eine strenge Zeitplanung. Nach dem Start läuft der Dienst auf der Kommandobrücke rund um die Uhr. Drei Gruppen und je zwei Männer halten auf der Brücke täglich acht Stunden Wache (mit Pausen selbstverständlich). Die Diensthabenden verfolgen den Kurs des Flüssiggastankers und die Situation sowohl auf dem Schiff als auch auf der See im Allgemeinen. Einmal standen auch wir Wache unter strenger Aufsicht von Roger Dias und Nikolai Budzinsky.
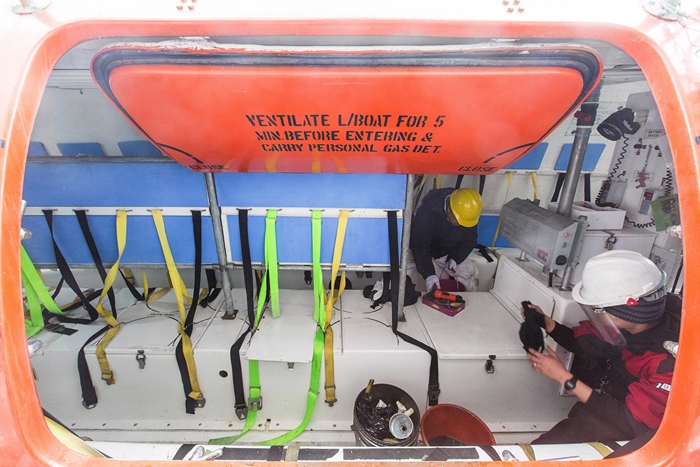
Die Mechaniker haben derzeit anderweitig zu tun: Sie überwachen nicht nur die Anlagen im Maschinenraum, sondern unterhalten auch die Reserve- und Notanlagen in einem arbeitsfähigen Zustand. So wechseln sie das Öl im Rettungsboot aus. Davon gibt es auf der Ob River zwei, die im Notfall je 44 Personen evakuieren können und mit einem benötigten Vorrat an Wasser, Speisen und Medikamenten bereits beladen sind.
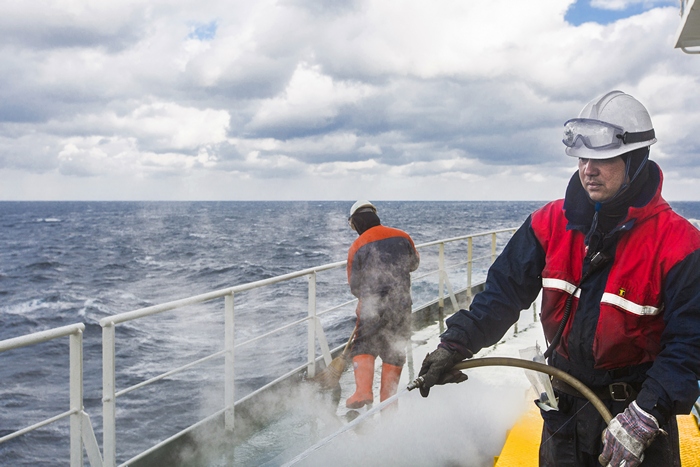
Matrosen reinigen inzwischen das Deck…
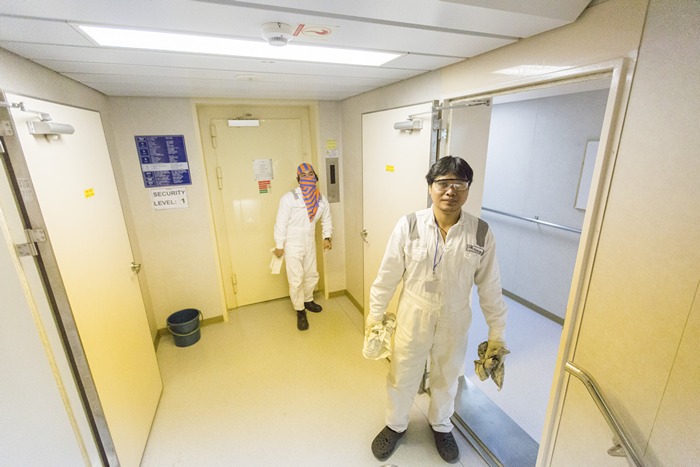
…und die Räume – Sauberkeit ist auf einem Schiff mindestens so wichtig, wie Disziplin.
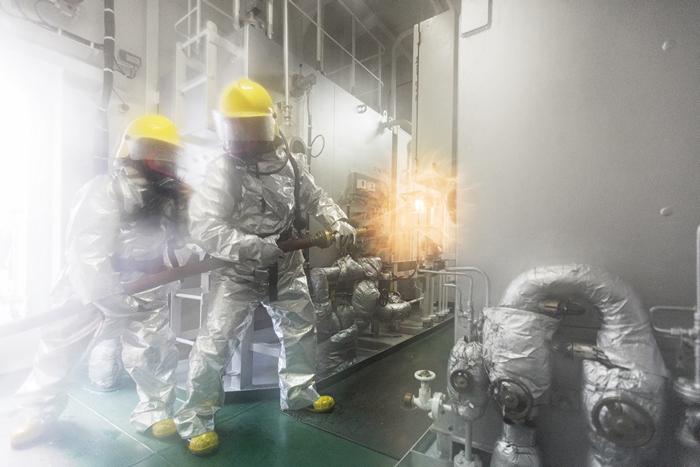
Nahezu tägliche Alarmübungen sorgen für Abwechslung bei der Routinearbeit. Daran nimmt die gesamte Besatzung teil, die sich für eine Weile von ihren Hauptbeschäftigungen ablenkt. Während unseres einwöchigen Aufenthaltes auf dem Tankschiff haben wir drei Alarmübungen beobachtet. Anfangs löschte die Besatzung ein angebliches Feuer in der Müllverbrennungsanlage.
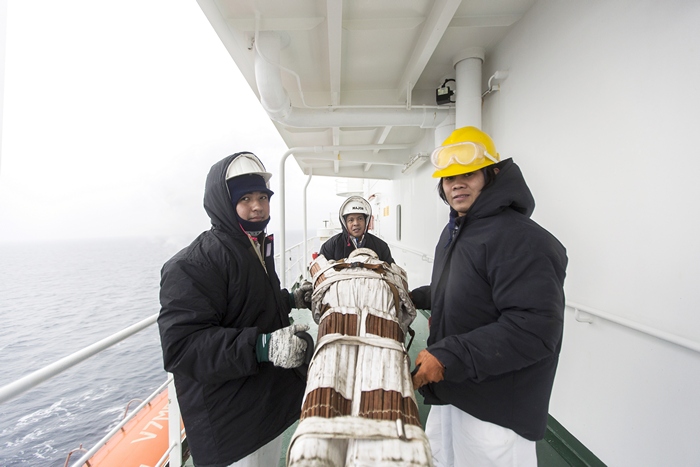
Danach rettete sie einen angeblichen Verletzten, der aus großer Höhe gestürzt war. Auf diesem Bild sehen Sie den geretteten „Menschen“: Er wird an das Ärzteteam weitergegeben, das den Verletzten ins Lazarett bringt. Die Rollenverteilung ist für die Alarmübungen nahezu dokumentiert. Das Ärzteteam leiten während dieses Trainings der Koch Ceazar Cruz Campana (Mitte) und dessen Gehilfen Maximo Respecia (links) und Reygerield Alagos (rechts).
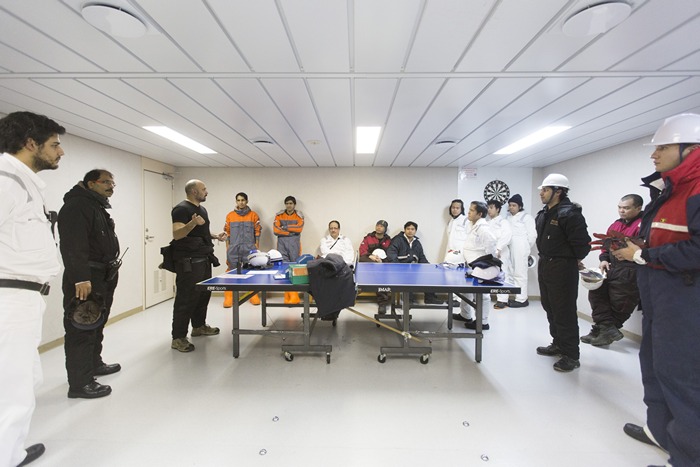
Bei der dritten Alarmübung wird nach einer vermeintlichen Bombe gesucht: Es erinnert vielmehr an ein Quest. Den Ablauf leitete der Erste Offizier Grewal Gianni (dritter von links). Die gesamte Besatzung wurde in Teams unterteilt, von denen jedes Karten mit einer Auflistung von Orten, die zu prüfen waren, bekam...

…und so begann die Suche nach einem grünen Karton mit der Aufschrift „Bombe“. Natürlich ging es darum, wer schneller war.
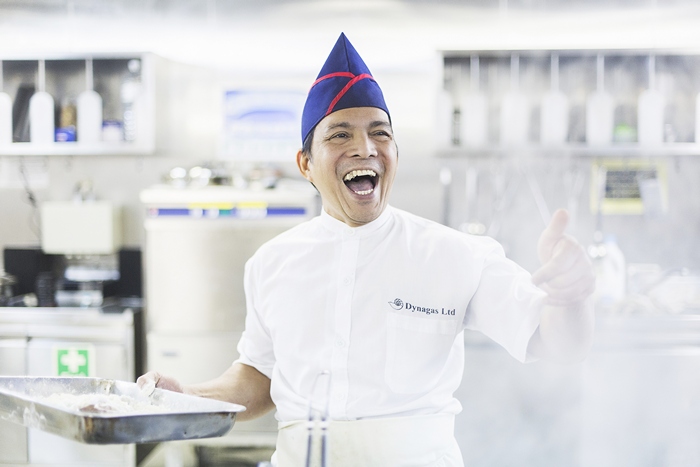
Dienst ist Dienst und Schnaps ist Schnaps. Für die drei Mahlzeiten täglich ist der Philippiner Cruz Campana zuständig. Sie haben ihn bereits auf dem Foto weiter oben gesehen. Dank seiner Profiausbildung zum Koch und seinen über 20-jährigen Berufserfahrungen macht er seine Arbeit spielend. Er gesteht, dass er in dieser Zeit durch die ganze Welt, außer Skandinavien und Alaska, gereist ist und sich mit den Essgewohnheiten eines jeden Volkes gut auskennt.
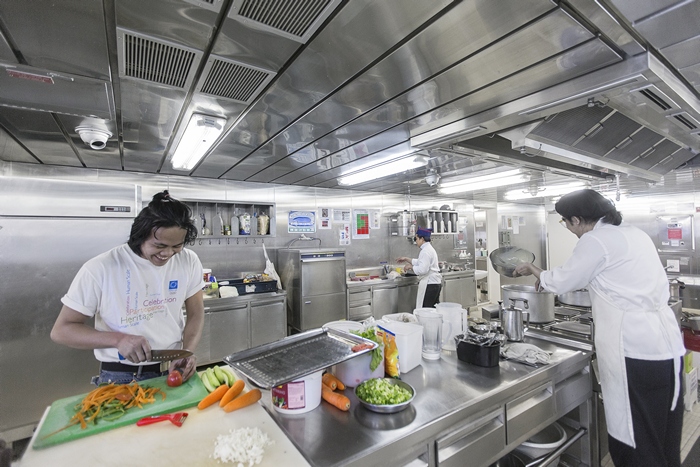
Kaum jemand ist der Aufgabe, so eine internationale Crew reichlich zu versorgen, gewachsen. Um jedem gerecht zu werden, bereitet er zum Frühstück, Mittag- und Abendessen Speisen aus der indischen, malaysischen und kontinentalen Küche zu. Dabei helfen ihm Maximo und Reygerield.
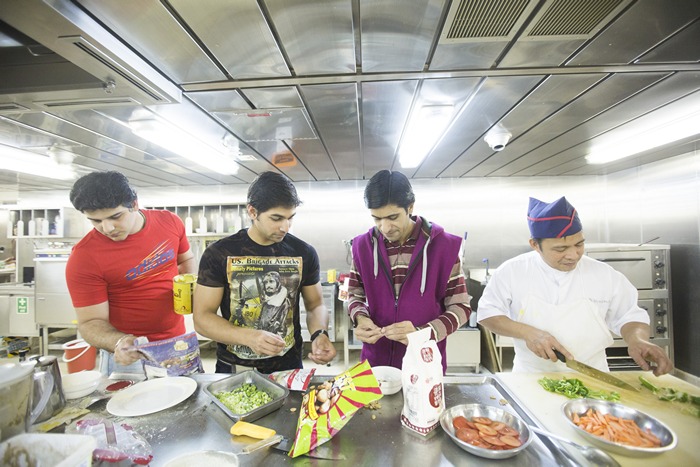
Mittlerweile statten auch Besatzungsmitglieder der Kombüse (so heißt die Küche in der Seemannssprache) einen Besuch ab. Sie haben zuweilen Heimweh und kochen selbst nationale Gerichte. Das tun sie nicht nur für sich selbst, sondern bewirten die gesamte Crew. Diesmal halfen sie bei der indischen Nachspeise Laddu, die Pankaj (links) zubereitete. Während der Koch Ceazar die Hauptspeisen für das Abendessen kochte, halfen Roger (zweiter von links) und Mohammad (zweiter von rechts) ihrem Kollegen die kleinen Bällchen aus süßem Teig zu kneten.
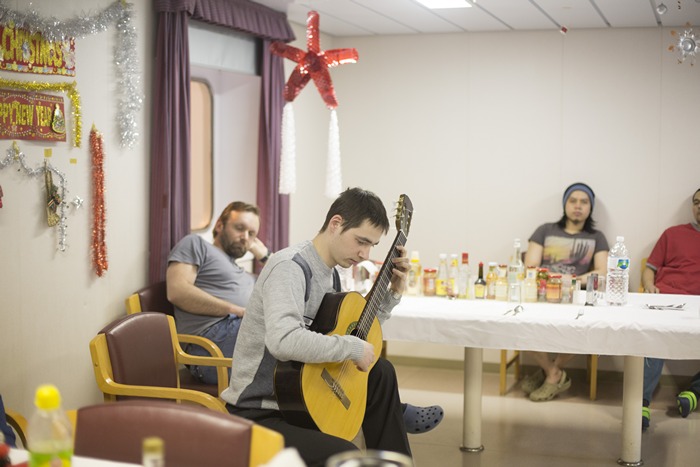
Die russischen Seeleute machten die ausländischen Kollegen mit ihrer Kultur durch die Musik vertraut. Der dritte Offizier Sergey Solnov spielt vor dem Abendessen russische Motive auf der Gitarre.
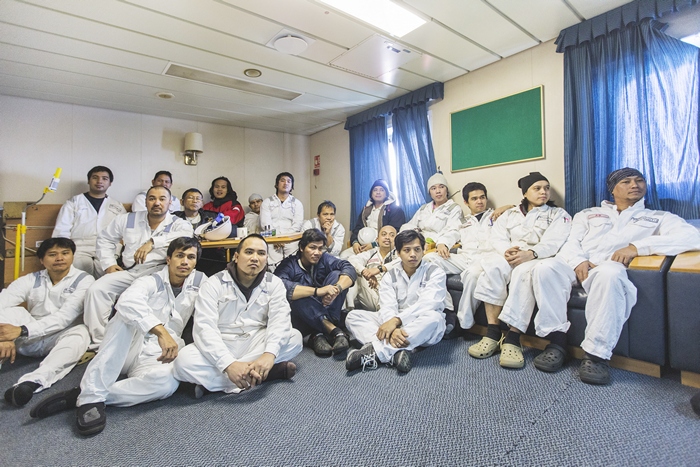
Gemeinsame Freizeitbeschäftigungen werden auf dem Schiff begrüßt: Die Offiziere leisten ihren Dienst drei Monate in Folge und die Matrosen – fast ein Jahr lang. In dieser Zeit sind alle Besatzungsmitglieder für einander nicht nur Kollegen, sondern haben sich angefreundet. An den Wochenenden (hier ist das der Sonntag: Jeder Einzelne wird seiner Funktionen nicht entledigt, aber die Besatzung bekommt möglichst wenig Aufgaben gestellt) werden gemeinsame Filmvorführungen, Karaoke-Wettbewerbe oder Mannschaftswettkämpfe in Videospielen veranstaltet.
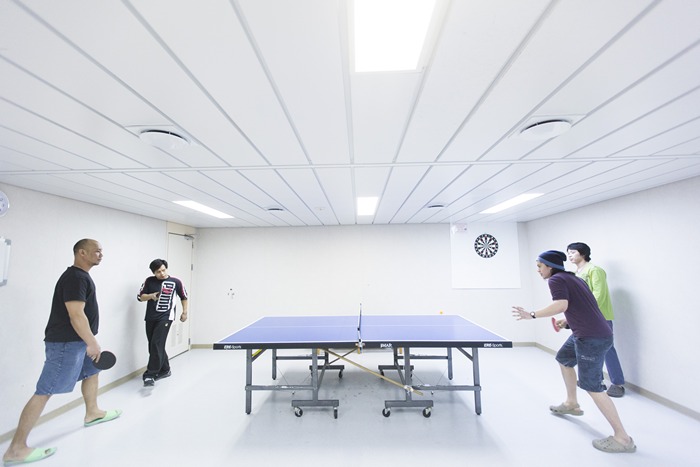
Aber am meisten gefragt sind hier aktive Freizeitbeschäftigungen: Auf hoher See gilt Tischtennis als die aktivste Mannschaftssportart. Die Besatzung veranstaltet regelrecht Tourniere am Ping-Pong-Tisch.
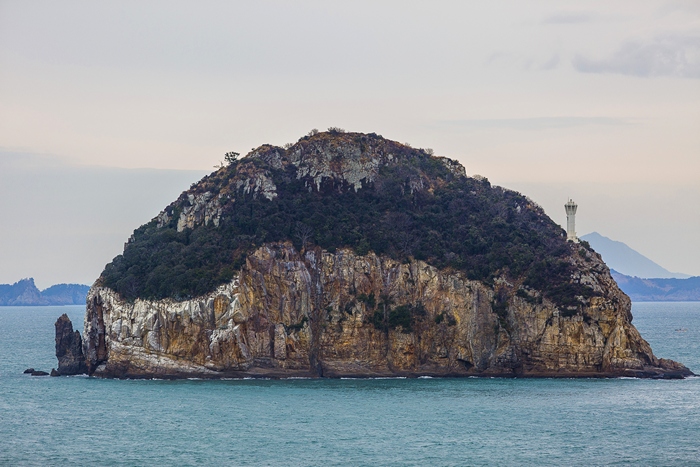
Derzeit ändert sich allmählich die bereits vertraute Landschaft, am Horizont ist Festland zu erkennen. Wir nähern uns der Küste von Südkorea.
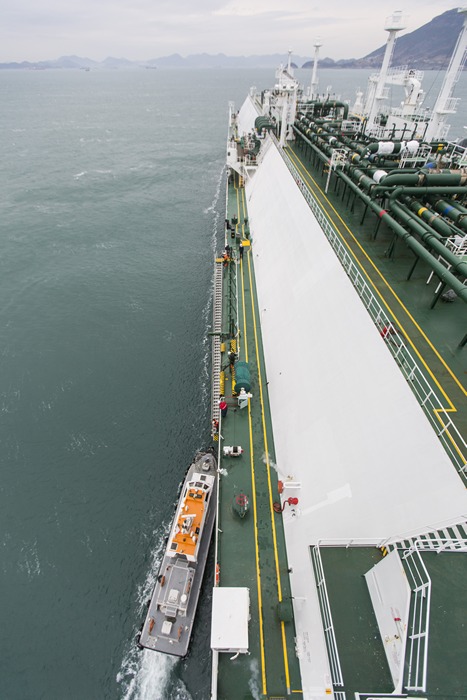
Die Matrosen beginnen die Taue zum Anlegen im Hafen vorzubereiten, hissen am Mast die Fahne von Südkorea (das gehört sich für Schiffe, die in die territorialen Gewässer eines anderen Landes einlaufen) und lassen die Strickleiter für den Lotsen hinunter.
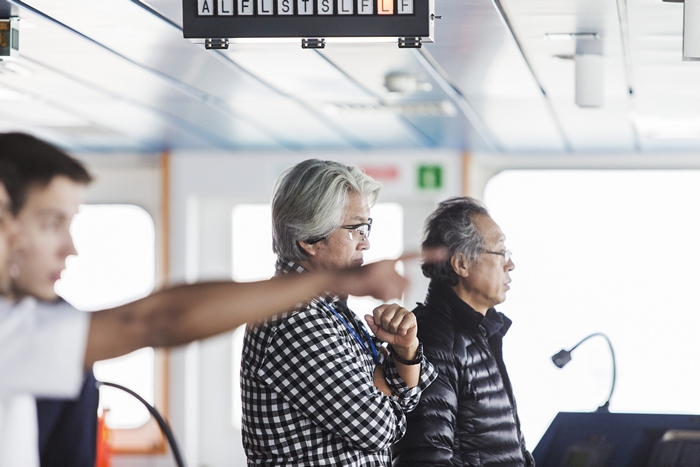
Der Lotse ist für die Manöver eines Schiffs in den Küstengewässern und für die Verbindung zum Hafen zuständig. Bis zur endgültigen Vertäuung des Schiffs wird er den Kurs des Tankers überwachen.
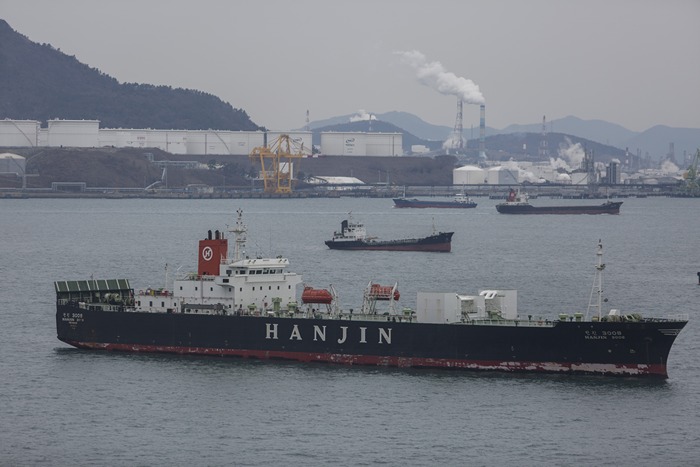
Sobald das Regasifizierungsterminal deutlichere Konturen annimmt, kommen dem Tankschiff vier Bugsierschlepper entgegen.
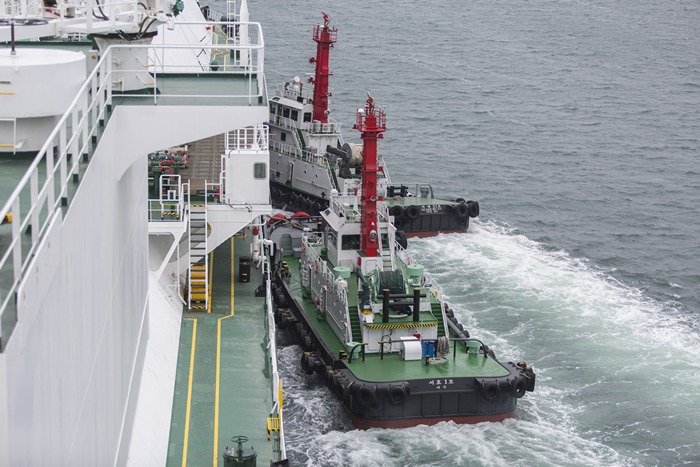
Sie drücken sich fest gegen den Schiffsrumpf und schieben den Tanker zum Pier. Anschließend werden an die Ob River Tankschläuche gekoppelt, die genauso aussehen wie auf Sachalin, und die LNG-Entladung beginnt. Sie nimmt eben so viel Zeit in Anspruch, wie die Befüllung des Tankschiffs mit Flüssiggas.
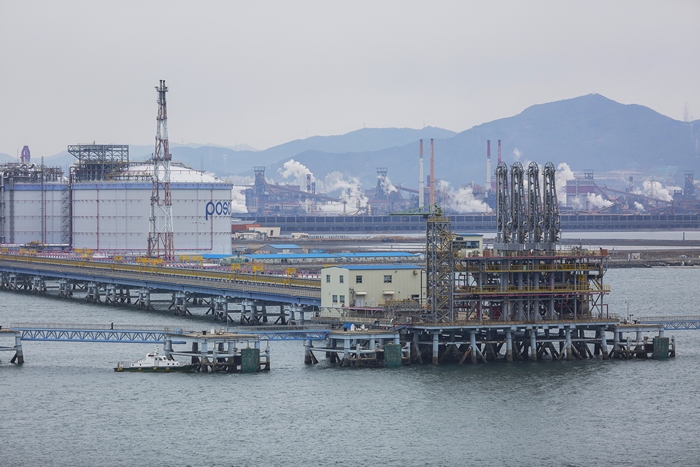
Damit ist der LNG-Transport abgeschlossen. Im Regasifizierungsterminal wird das LNG wieder in einen gasförmigen Zustand versetzt und an die südkoreanischen Verbraucher ausgeliefert.
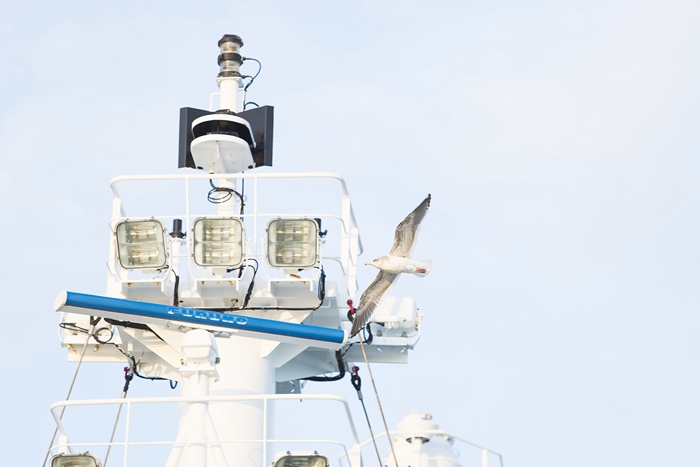
Die Ob River kehr mit vollständig geleerten Tanks auf Sachalin zurück, um eine neue LNG-Lieferung abzuholen. Welches asiatische Land der Flüssiggastanker anlaufen soll, wird meistens erst kurz vor der Befüllung des Schiffs mit russischem Erdgas bekannt.
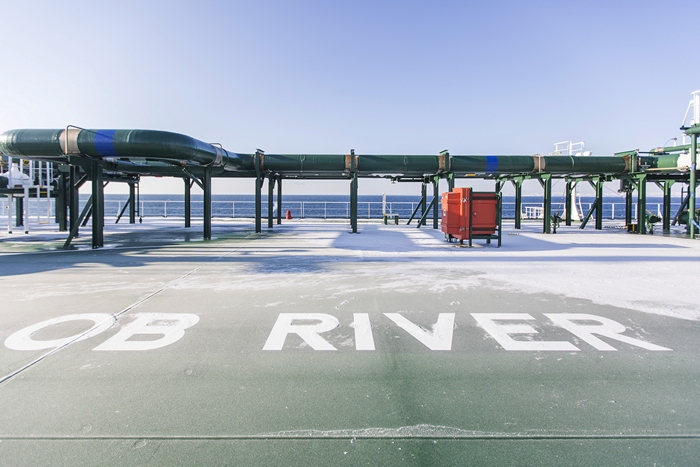
Unsere Gas-Tour ist zu Ende. Indessen laufen die LNG-Geschäfte der Gazprom auf Hochtouren und werden mit einer Geschwindigkeit ausgebaut, die der eines riesigen Flüssiggastankers gleichkommt. Wollen wir diesem großen „Schiff“ eine gute Seereise wünschen.
P. S. Die Foto- und Videoaufnahmen wurden nach allen Sicherheitsvorschriften gemacht. Wir danken den Kollegen der Gazprom Marketing & Trading und der Sakhalin Energy für ihre Unterstützung bei den Dreharbeiten.